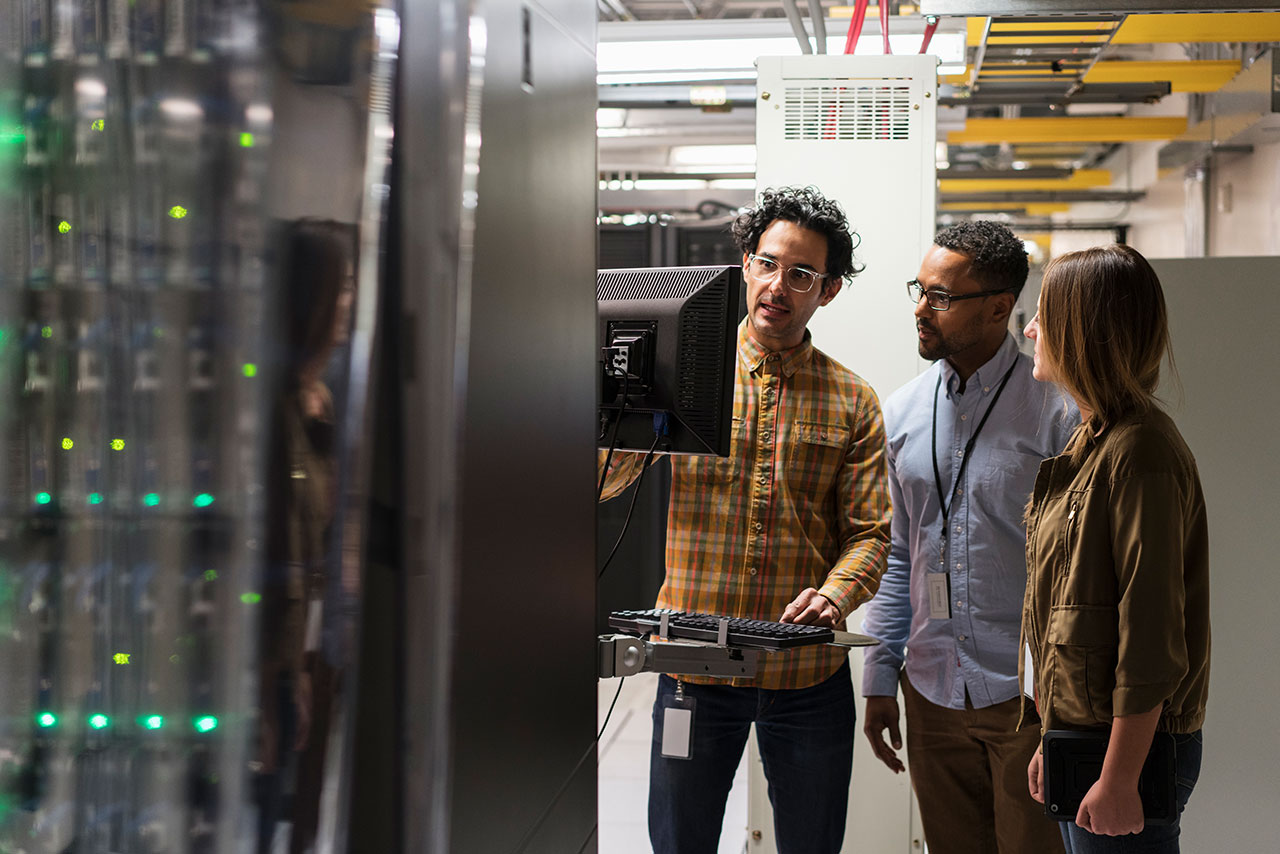
Unlocking the Business Value of Industry 4.0: Part 5
The pandemic of 2020 has led to digital acceleration. “We’ve seen two years’ worth of digital transformation in two months,” said Microsoft CEO Satya Nadella during a quarterly earnings call in the spring of 2020.23
“The disruption and economic hardship caused by the ongoing pandemic have increased the urgency to accelerate smart manufacturing initiatives for future competitiveness,” according to Deloitte.24 In a recent CEO poll by the Manufacturers Alliance for Productivity and Innovation (MAPI), 85% of leaders expected investment in smart factories to rise by June 2021.25
To combat the pandemic, manufacturers installed computer vision systems to enable virtual plant tours for customers, added wearable devices for line workers to signal when they were crossing into a coworker’s six-foot personal space zone, and added collaborative robots (cobots) to augment their workforces, according to Deloitte. Caterpillar’s sales of autonomous technology for mining operations grew at a double-digit percentage in 2020 compared with the year before, according to Reuters.26 Oil companies have been relying on edge computing solutions at well sites so that engineers can steer the drill bits from their offices or, increasingly, their homes.
But the pandemic is also creating a gap between the leaders in smart manufacturing and the rest of the field. Sixty-two percent of manufacturers surveyed in July 2020 are moving ahead with their smart manufacturing investments, allocating even more to such initiatives than they did in 2019.27 However, 38% of manufacturers paused their smart factory investments as they assessed the impact of the economic conditions caused by COVID-19, according to Deloitte.
Deloitte stresses the importance of forming an ecosystem of solution providers to successfully accelerate smart manufacturing initiatives. Given the complexity of Industry 4.0, most manufacturers do not have capabilities in all areas. Ecosystems of state-of-the art solution providers can support a more rapid transition to adaptive manufacturing. The difference between having relationships with partners and vendors and having an ecosystem is that the ecosystem approach requires deliberate coordination among and between various parties. And, as in a biological ecosystem, all players may share the same fate.
The Deloitte and MAPI smart manufacturing ecosystem research identifies eight major use cases for a production ecosystem and the number of manufacturers currently operationalizing them. The study reveals that while 68% of manufacturers surveyed connect with a production ecosystem, each use case is currently operationalized by between just a fifth and a third of manufacturers surveyed. A deeper look at survey data reveals that companies that had external partners were operational, on average, across 31% of the use cases they were implementing, compared with just 15% for those that start with in-house development, according to Deloitte.
Verizon tapped into an ecosystem to initiate the world’s first completely virtualized 5G data session — from the network core to the radio access network (RAN) and the edge of the network. Its ecosystem partners included Samsung, Intel, and Wind River. Samsung’s 5G virtualized RAN hardware and radio units were integrated with Wind River platform and container-based middleware as well as the Intel Xeon Scalable processor, field-programmable gate array (FPGA) acceleration card, Ethernet network adapter, and software reference architecture.28
Bill Stone, VP of technology development and planning at Verizon, described a mature, collaborative, and innovative ecosystem when he discussed the partnership in a phone interview with SDxCentral: “It was a combination of selecting the best-in-class vendors that supplied the necessary components, having them develop to our requirements, then bringing them together in the lab environment to conduct integration testing, bringing that into our own Verizon lab environment, and then moving into field tests, all of which came together for the main production into the live network.”29
The Deloitte and MAPI study lists the top five partners contributing the most value to manufacturers’ ecosystems, starting with IT software vendors, Industry 4.0 technology providers, operation technology vendors, physical automation/robotics vendors, and professional services firms.
Manufacturers with an ecosystem approach to smart manufacturing are about twice as likely to see an increase in their pace of introducing new digital products and services in the market, an expansion of innovation capacity in the company, acceleration in digital maturity of the company, and a reduction in operational costs through greater efficiencies.30
Eight Use Cases for a Production Ecosystem
and the Share of Manufacturers Operationalizing Them
Source: Deloitte/MAPI31