The Fourth Industrial Revolution signals a business shift
Manufacturing is increasingly software driven, blurring the lines between the physical world of machines and the cyber world of data and disrupting traditional manufacturing paradigms.
“While previous industrial revolutions have been around a new source of energy, the Fourth Industrial Revolution is going to be about fundamental shifts in business models,” says Fred Rio, worldwide product manager at Caterpillar’s Construction, Digital, and Technology division.1
These paradigm shifts are due to the digital transformation of the industrial sector. After years of digital transformation associated with IT — focusing mostly on information flow in the digital ether — the focus has now turned to IoT. McKinsey’s Digital Manufacturing Global Expert survey reveals that most manufacturing companies (68%) consider Industry 4.0 manufacturing initiatives to be their top priority.2 The global industrial automation market is expected to reach US$326.14 billion by 2027 after a decade of CAGR at 8.9%, according to Fortune Business Insights.3
McKinsey puts the value creation potential of manufacturers and suppliers implementing Industry 4.0 in their operations at $3.7 trillion by 2025.4 This economic value will be unlocked by manufacturers who replace traditional manufacturing paradigms with adaptive manufacturing by embedding their production facilities with advanced data-generating and processing software. The insights gathered from a network of connected devices can be harnessed to increase productivity and develop value-add, outcome-based services — creating new, more profitable business models.
Almost a third (30%) of global factory budgeting is earmarked for smart factory initiatives, ranging from quality sensing and detecting through asset intelligence and performance management to command centers, factory synchronization, and real-time asset tracking.5 Investment in smart factory initiatives pays off. “Trailblazers are pioneering factory-related innovation, dedicating a whopping 65% of their global factory budget to smart factory initiatives,” according to The Wall Street Journal.6 “Trailblazers report 20% average improvement in production output, factory capacity utilization, and employee productivity over the past three years.”
Build and lead a focused ecosystem of technology partners
For cohesion and seamlessness, the entire technology stack process, from development to rollout, must be tightly managed. Manufacturers should track three aspects of the process:7
Architecture complexity: Challenges arise in navigating the complex landscape of solution providers. When building in the technology stack’s needed components, machinery manufacturers should fully leverage industry standards to ensure interoperability across different organizations.
Partnerships: Select a few partners with deep functional and integrative expertise, and codevelop when possible. More than 40% of respondents say they prefer to build their IT/OT systems in-house or tailor them based on external sources. This adds to the need to bridge a wide range of in-house, purchased, and codeveloped systems.
Agile execution: Manufacturing companies should bring an agile mindset to software and analytics in their digital initiatives. In addition to forming reliable external partnerships, they need to support internal collaboration across functions and break down organizational silos.
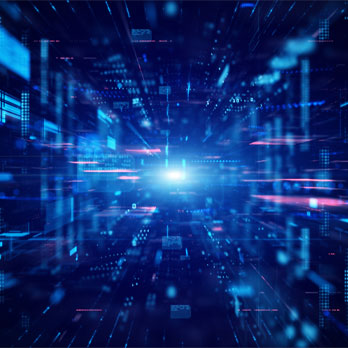