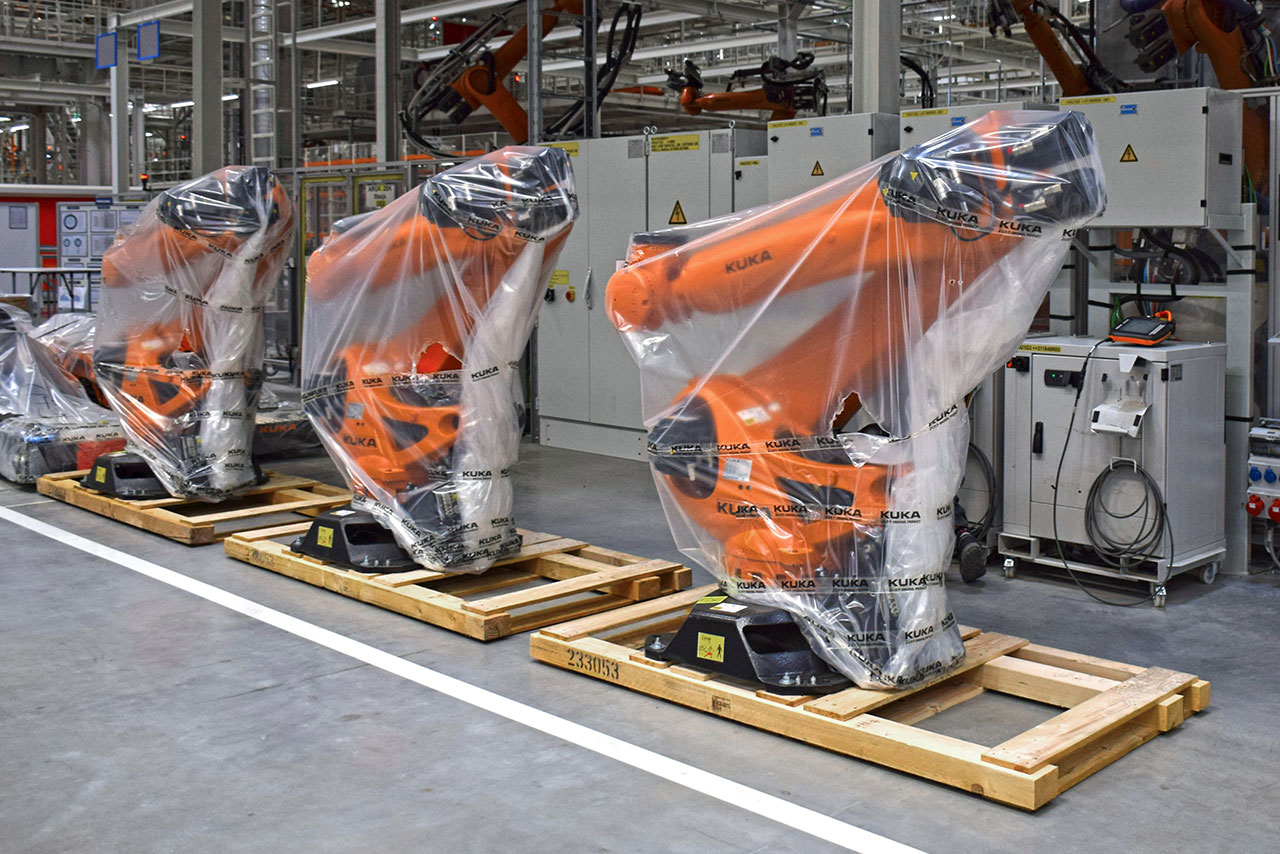
Unlocking the Business Value of Industry 4.0: Part 3
For many organizations, intelligent adaptive manufacturing has proven challenging to implement. McKinsey’s report “Digital Manufacturing — Escaping Pilot Purgatory” reveals that while digital manufacturing pilots are common, company-wide rollouts are still rare. For instance, while around two-thirds of industrial companies have piloted connectivity, intelligence, or flexible automation initiatives, less than a third of such initiatives have been implemented.16
Transitioning to digital manufacturing is a tall order, since most organizations are updating existing assets and processes rather than starting from scratch. Industrial manufacturing is full of legacy systems, many 20 or 30 years old, reaching the end of their lifecycles. Some parts need to be swapped, but the newer technologies must be able to function within the legacy asset. A Wind River survey confirms that among the biggest barriers to deploying needed technologies are “need to upgrade or reengineer legacy systems” (35%) and “need to retrofit devices” (31%).17
Software-driven factories create risks. OT is part of a real-life, physical environment. An interruption could be catastrophic, so new technologies must be implemented while the whole system is operational. A mistake on a production line can lead to expensive downtime, or, worse yet, harm to a human being. “The only way to maintain the integrity of the devices generating the interactions and the exchange of data is to build security in at each stage of the product lifecycle: design, development, deployment, and operations,” according to a report by Wind River.18
Finding the right technology partners and systematically addressing legacy assets, inoperability, and security concerns up front is key to transitioning to digital manufacturing. McKinsey has identified the following principles for forming the comprehensive technology stack and working with technology partners.
16 Digital Manufacturing – Escaping Pilot Purgatory, Digital/McKinsey, 2018
17 “5G and Industry 4.0: Where Promise Meets Reality” (web seminar), Wind River, November 17, 2020
18 “Secure Through The Lifecycle,” Wind River
Form the Comprehensive Target-State Technology Stack19
Digital manufacturing is, by definition, technology driven. In determining the optimal technology stack, manufacturing companies should keep five characteristics in mind:
1 / Comprehensive: The definition should include a look at all five layers: collection, connectivity, data, analytics, and applications. It should also be specific to your operational model.
2 / Scalable: A critical element for scalability is the data ingestion pipeline complemented by analytic capabilities.
3 / Analytics enabled: Systems (software and infrastructure) provide the material, but analytics provide the insights that, ultimately, generate the value.
4 / Integrated: Digital manufacturing implementation requires that the relevant information from operational (OT) and information technology (IT) be integrated. Successful IT/OT convergence creates the delivery engine that will develop use cases that meet a manufacturer’s business needs.
5 / Secure: Cybersecurity must be actively addressed by, for example, analyzing the connections and adaptability between legacy and future systems.
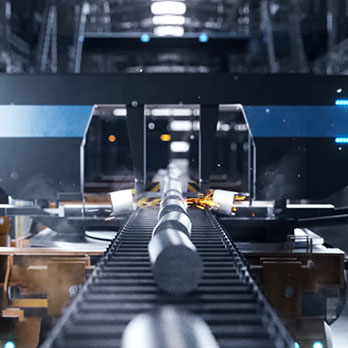