Building Faster Safer Responsive Robots for the Edge
Wind River and Intel Meld Technologies to Deliver Functional Safety, TSN Capabilities, and More
INTRODUCTION
Next-generation industrial robots and advanced control automation capabilities are enabled effectively by a real-time operating system from Wind River® — VxWorks® — and the 11th Generation Intel® Core™ processor family, designed for IoT platforms and demanding industrial applications.
ACHIEVING INDUSTRY 4.0
Enabling the requisite level of responsive interactivity and frictionless interoperability needed to realize the vision of Industry 4 .0 manufacturing technology and industrial IoT platforms requires hardware and software engineered for the demanding infrastructure edge . Two components that satisfy these requirements and interoperate smoothly are Wind River VxWorks and the 11th Gen Intel Core processor for IoT platforms . VxWorks, widely recognized as the industry’s leading real-time operating system (RTOS), supports the fast, deterministic decision-making necessary for industrial applications at the edge . The design features included in the 11th Gen Intel Core processor unlock Time-Sensitive Networking (TSN) capabilities and satisfy strong functional safety requirements . Together, the hardware and software interoperate fluidly to ensure high-availability operation, low-latency communication, and deterministic decision-making . Safety-certified components on both the hardware and software sides streamline solution certification across a broad swath of industry standards.
“Ultimately, TSN is an enabling technology to support the convergence of IT (information technology) and OT (operational technology) over a cost-effective, standard, nonproprietary Ethernet network that drives higher productivity and reduction in cost across many industrial use cases. The key to its successful adoption is interoperability.”1
— Andrei Kholodnyi, Janus Yau, Markus Carlstedt
THE RISE OF AUTONOMOUS SYSTEMS
An article posted by the World Economic Forum2 highlighted the successful SpaceX launch and fully automated docking of the Crew Dragon spacecraft with the International Space Station as a milestone in more than one way . This event marks the start of a new era in space travel, but it also signifies a major step forward in the technologies that enable autonomous systems.
Enabling machines to perform tasks efficiently without human intervention, freeing workers from repetitive tasks, is clearly one of the benefits, but the ability to function in real time is vital to autonomous systems. In many cases, low-latency communications between network nodes and devices is an essential requirement . 5G networking factors in as a component of real-time solutions . As the WEC article noted, “Today’s automation is an ever-present engine in various fields. It enables the high bandwidth and low latency 5G requires for the effective use of drones and self-driving cars, for example . It’s needed to operate farm tools and program robots that deliver prescriptions at pharmacies . It controls cloud robotic arms and Internet of Things components . And it is key for security of networks and services to protect user and data from cyberattacks . Simply put, it is essential to operating cutting-edge technologies in this age of the Fourth Industrial Revolution.”
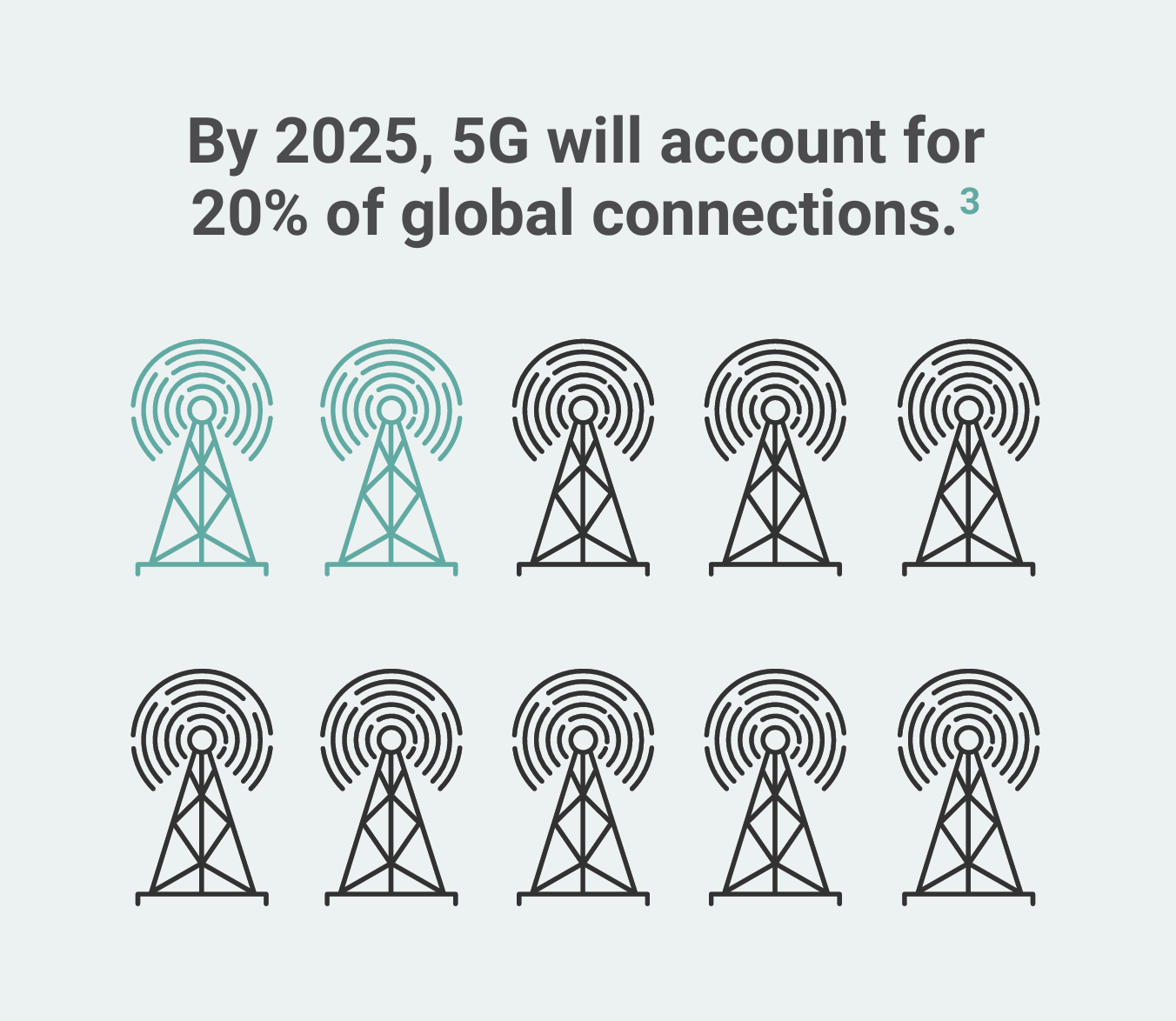
AT THE INTELLIGENT EDGE, TIMING IS KEY
Effective IoT deployments require not only low-latency communication among machines, devices, and sensors but also a mechanism to coordinate and orchestrate activities so that operations can be performed in a synchronized, predictable way . Brian McCarson, VP, Internet of Things Group, Intel, explained the concept in an episode of Intel’s Inside IoT: “So, now, think about a smart manufacturing example . You’ve got robots communicating with robots . And if a robot is going to hand one part over to another robot, how are they going to work together to make sure that the handoff occurs perfectly? This is where the concept of TSN and TCC [time-coordinated computing] is critical to unlocking and unleashing the full potential of all your IoT devices in real-world deployments.”4
In an interview with Enterprise IoT Insights, Kun Wang, system manager for digital services at Ericsson, talked about the role of TSN in industrial automation . “TSN is the Industry 4 .0 enabler . In fact, TSN enables more robust and reliable Ethernet communication between machines and plants, even under high network loads . Since network resources can be reserved for time-sensitive traffic in the TSN network, data transmission is guaranteed, and it is precisely predictable regardless of the load . Today a large variety of f ieldbuses — real-time Ethernet protocols on factory shop floors — make the interconnectivity need for Industry 4.0 difficult to achieve. To overcome this issue, the IEEE 802 .1 TSN Ethernet standard family was introduced for real-time deterministic, enterprise-wide, low-latency industrial communication.”5
While 5G helps build responsive, real-time networks for industrial IoT solutions, the software operating system and system hardware are also critical parts of these types of solutions . Wind River and Intel components work in concert to deliver the enabling technologies . The 11th Gen Intel Core processor for IoT platforms is the core of a system-on-chip (SoC) tailored for industrial and IoT applications . The SoC’s capabilities dovetail neatly with the industry’s premier real-time operating system, VxWorks, with built-in support for TSN . The complementary capabilities, as well as many shared safety certifications that strengthen industrial deployments, make the Intel SoC and VxWorks well suited for a broad slate of Industry 4 .0 implementations in which network timing, robotic coordination, and precision communications are required.
“We have architectural features built in specifically for both of us [Wind River and Intel] with technologies — time-coordinated computing, Time-Sensitive Networking, error code correction, reliability features, integrity features — to help our customers build their applications and solutions.”
— Ganesh Kondapuram, Platform Architect for Intel IOTG
WHAT IS TIME-SENSITIVE NETWORKING?
Industrial automation began in earnest in the 1980s, relying on a hierarchical structure, the Purdue model, for segmenting communication into separate layers and defining the processes through which machines interact and function . Although this model served the industry well and made deterministic networking and computing possible, the present IoT-era data flow is more complex, and a hierarchical structure does not effectively deliver the timing and low-latency communication required by modern automated control systems.
IEBmedia .com expresses the essential challenge in these terms: “Although independent purpose-built protocols may be very good at automating the original tasks for which they were developed, they are essentially speaking different languages, which results in real time communication difficulties. Traditional industrial networks in this model are also tuned for latency and control, unable to ‘share the wire,’ and are often limited to 100 Mb/s (or lower) transmission speeds.”6
In response to this challenge, in November 2012 the Time-Sensitive Networking Task Group of the IEEE 802 .1 Working Group initiated development of standards to provide synchronized data movement with precision timing over deterministic Ethernet networks. This TSN task group has focused on establishing quality-of-service (QoS) guarantees to ensure that mission-critical traffic and applications are successfully transferred over the network and that time-sensitive transactions are handled smoothly, offering a toolbox that encompasses four individual categories: reliability, time synchronization, resource management, and traffic shaping. Through techniques that include traffic shaping and queuing, the IEEE 802.1 standards provide a framework for reliable communications in environments in which deterministic decision making takes place. Figure 1 shows the IEEE 802.1 AS timing and synchronization for time-sensitive applications.
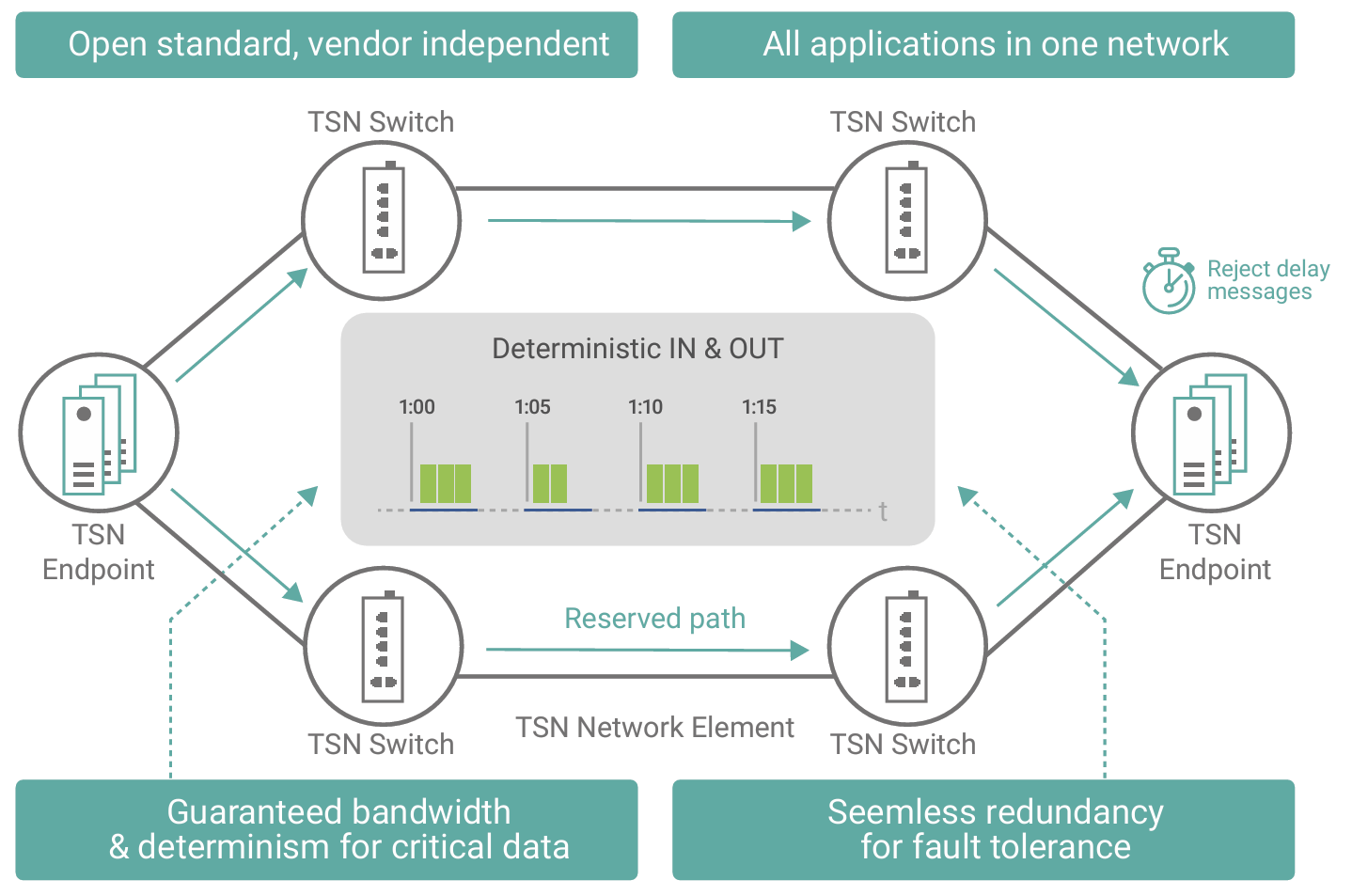
INSIDE THE SOC FOR IIOT SOLUTIONS
With the launch of the 11th Gen Intel Core processor family for IoT platforms, Intel extends its commitment to the future of Industrial IoT, with capabilities and built-in features that address key issues when implementing autonomous system designs and deploying industrial robots on the network edge.
The SoC for IoT platforms, at the heart of which is the 11th Gen Intel Core processor, offers these features for developing reliable, efficient IIoT solutions:
- Time-coordinated computing (TCC): At the hardware level, TCC provides time synchronization and timeliness within Intel SoCs, synchronizing hardware and software . It helps real-time applications meet performance metrics, including worst-case execution time (WCET).
- Time-Sensitive Networking (TSN): Support for network TSN operations is handled by a platform controller hub integral to the 11th Gen Intel Core processor with a separate Ethernet controller and an Ethernet TSN controller. This feature has been co-engineered and tested for interoperability with VxWorks.
- Extended temperature range: For use in harsh environments, this ruggedized version of the SoC can be used in embedded solutions with temperatures ranging from -40° C to over +100° C.
- In-band error correction code (IBECC) support: Providing error check and correction protection to all regions, or any specific regions, of the physical memory space, IBECC support improves accuracy and reliability.
- Functional safety design packages: These packages provide collateral to help customers build safety solutions and certify their end product.
- Certificate evidence and certificates: Documentation is provided for the following safety certifications: CertCore 178, DO-178C certification evidence; CertCore 254, DO-254 certification evidence; CertCore 26262, ISO 26262 accredited safety assessment certification; ARP4761 FMEA.
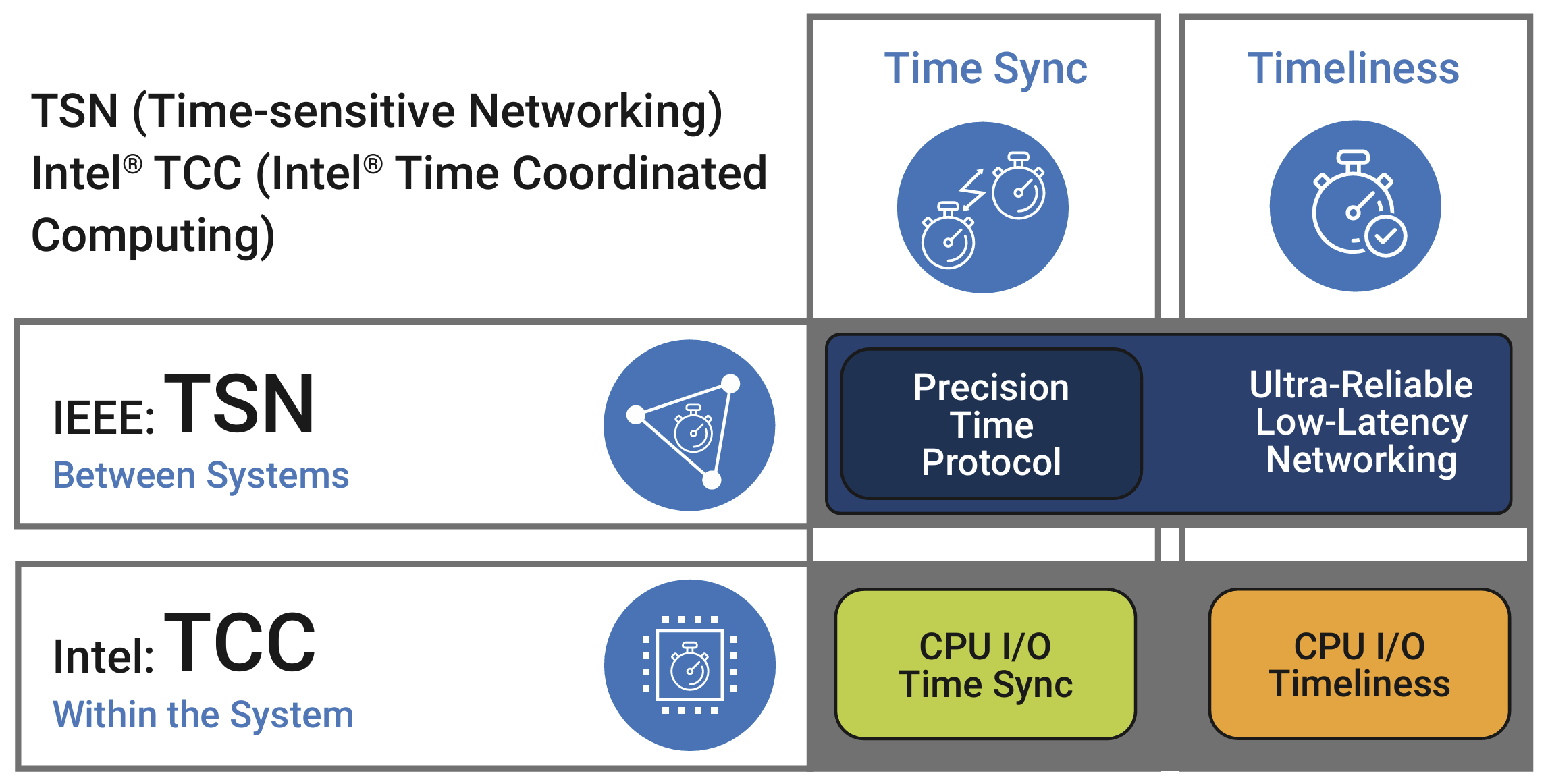
VXWORKS: A REAL-TIME OPERATING SYSTEM FEATURING TSN
VxWorks occupies a unique niche in the industry, positioned in a role that is especially well suited to the escalating adoption of industrial robotics and autonomous systems on the intelligent edge.
Key features include:
- Support for TSN: VxWorks has implemented TSN, guaranteeing real-time communication and packet delivery within a bounded time or latency on a switched Ethernet network.
- Wide-ranging multi-core and multiprocessing support: Hardware support ranges across 32-bit and 64-bit architectures, including architectures from Intel, Arm®, Power, and RISC-V.
- Container support: The latest version of VxWorks supports container technology for application updates and patches.
- Extensive available security provisions: With a security framework that maps to the CIA Triad, VxWorks integrates protection into the full spectrum of OS operations. From initial system startup to shutdown procedures, system architects can tap into whatever level of security is appropriate to application needs and potential risk vectors.
- Compliance with a wide range of certification standards: Supported standards include DO-178C, IEC 61508, ISO 26262, ARINC 653, POSIX®, and FACE™. Compliance is achieved on commercial off-the-shelf (COTS) systems and supported by safety certification evidence.
Jeremy Pollard, writing for Control Design, said, “TSN will make processes predictable and reliable and will have control over the latency of real-time critical data that the process needs to deliver to the infrastructure . And we [the IEEE 802.1 TSN Task Group] want to do it with vendor independence . We have that now to some extent with standard Ethernet, but with the new protocols that will be developed, running a variation of devices over the same pipe and the same protocol has its advantages.”8
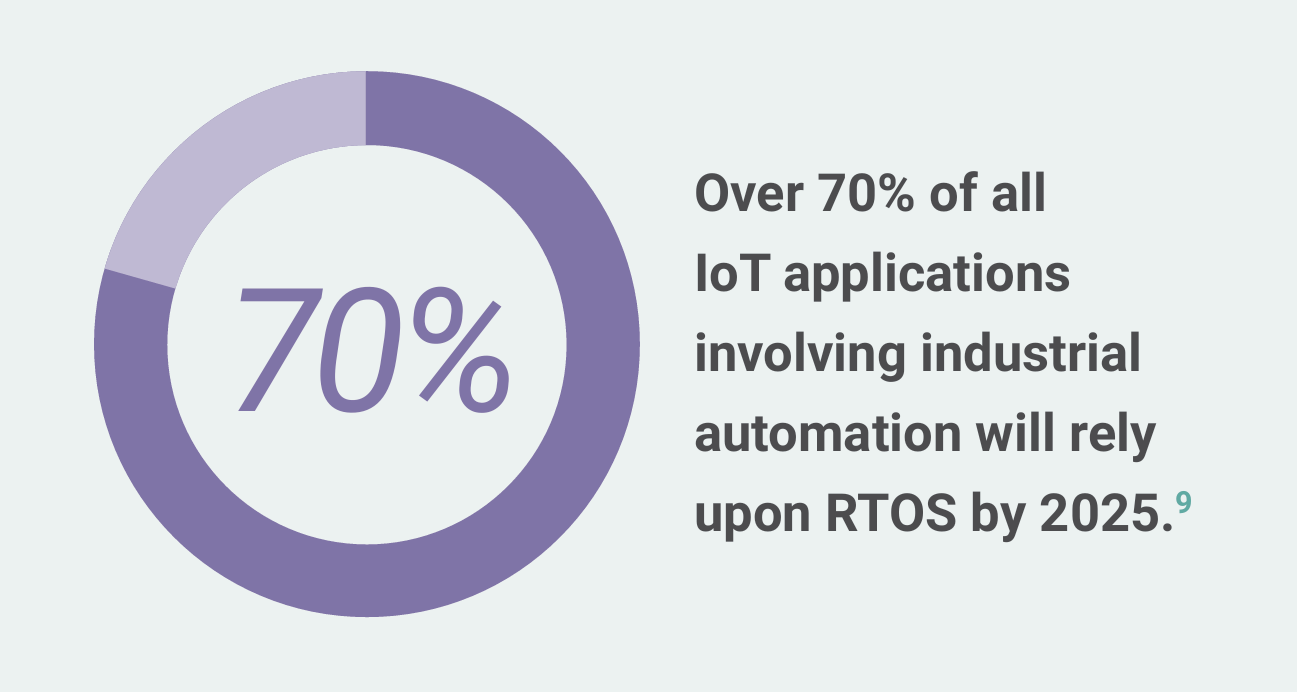
ENABLING AUTONOMOUS SYSTEMS AT THE EDGE: WIND RIVER SOLUTIONS
Tools and solutions from Wind River help accelerate robotics development and automated control processes at the intelligent edge, combining expertise in 5G networking, container technology, embedded solutions running on a real-time operating system, artificial intelligence, machine learning, and simulations of complex systems for testing and development.
For developing control automation equipment, industrial robots, and manufacturing solutions, Wind River delivers the tools and technologies that enable high-performance, reliable, certified solutions.
TSN technologies offer a scalable, predictable approach to deterministic networking over standard Ethernet. But TSN is more a toolbox than a single, comprehensive solution, so system integrators must rely on independent vendors and multiple protocols to satisfy the specific requirement for each industrial application. This predicament is why interoperability is the key to ensuring the success of TSN adoption.10
Wind River Studio
This cloud-native platform is a secure foundation for the development, deployment, operations, and servicing of vital intelligent edge systems . Optimized for DevSecOps, Studio enables application teams to employ continuous integration (CI) and continuous delivery (CD) workflows, drawing on agile development practices . These capabilities are paramount to the future of intelligent machines and responsive cloud-based infrastructures.
VxWorks
The world’s leading commercial real-time operating system (RTOS), VxWorks now includes support for container technology, providing an effective means for keeping applications up-to-date on the intelligent edge . Well suited to high-performance IIoT applications, VxWorks is a mainstay in process control automation, robotics, and intelligent vehicle applications. To support industrial implementation, certifications are in place for IEC 61508SIL 3, ISO 26262 ASIL D, and IEC 62304.
Solutions from Wind River help accelerate the development of intelligent edge applications, powering industrial infrastructures and delivering proven reliability . Our customers rely on our deep industry experience to support edge computing and 5G, complementary technologies that are turning the vision of intelligent IIoT solutions into a reality.
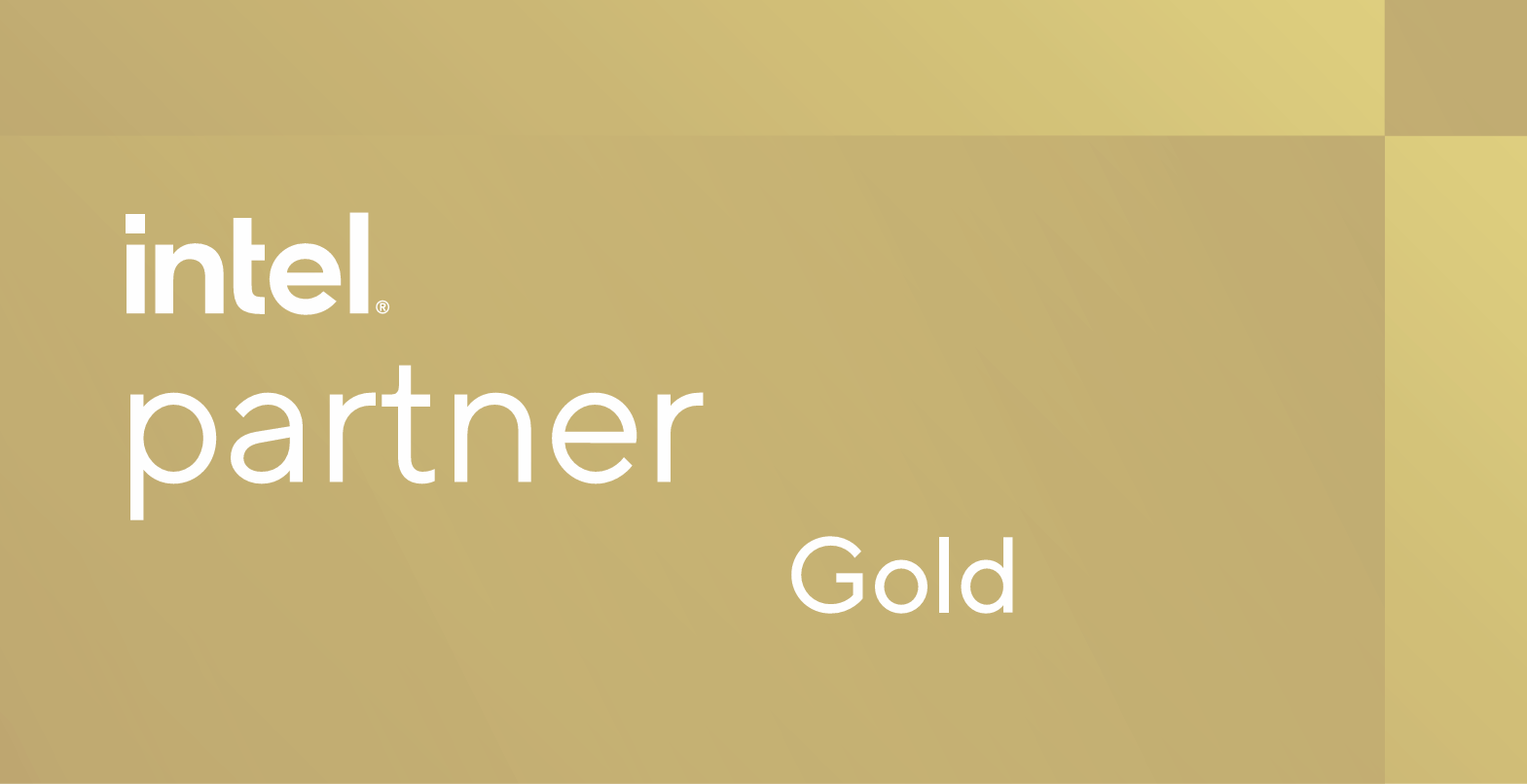
Intel Partner Alliance Member
Wind River is a long-term member of the Intel Partner Alliance, a program developed to unify members across a cooperative, collaborative environment for planning, designing, and building innovative solutions . Wind River is particularly active in the Intel IoT Solutions Community, working with other members within a strong and dynamic ecosystem.
ADDITIONAL RESOURCES
For a demonstration of how to run a TSN application on VxWorks, presented by Andrei Kholodnyi, principal technologist, Technology Office in the office of the CTO, Wind River, visit the Deeper Dives with the Wind River Tech Team web seminar series.
To learn more about the full lifecycle management of intelligent systems, visit Wind River Studio Developer Capabilities.
To learn about the latest advances in robotics technology, visit “On the Cutting Edge: Robots Join the Sensor-Driven Revolution."
REFERENCES
- Andrei Kholodnyi, Janus Yau, Markus Carlstedt, “TSN and Real-Time Operation from Wind River,” March 4, 2020
- Aron Heller, Abhay Savargaonkar, “The Rise in Automation and What It Means for the Future,” World Economic Forum, April 2021
- The Mobile Economy 2020, GSMA
- “Intro to Time-Sensitive Networking and Intel Time Coordinated Computing (Intel TCC),” Inside IoT with Brian McCarson, Intel
- James Blackman, “What Is TSN and Why Industrial 5G Won’t Work Without It,” Enterprise IoT Insights, June 2021
- How TSN Is Revolutionizing Industrial Automation, Industrial Ethernet Book, March 2021
- How TSN Is Revolutionizing Industrial Automation, Industrial Ethernet Book, March 2021
- Jeremy Pollard, “TSN: Where IT and OT Converge,” Control Design, July 28, 2020
- IoT Real Time Operating Systems (RTOS) Market by Components, Processor Type, OS, Segment, and Industry Verticals 2020 – 2025, Mind Commerce, 2020
- How TSN Is Revolutionizing Industrial Automation, Industrial Ethernet Book, March 2021