Evolve Control Automation Management Capabilities for Industry 4.0 Benefits
Workload Consolidation Extends System Functions to Gain Cost Savings and Data Analytics and Meet High Safety and Security Standards
THE RESULT
Using the Helix Platform hypervisor together with VxWorks, Wind River Linux, and Wind River development tools, a work load consolidation solution for control automation for a fac tory machine can be developed for a wide variety of industrial manufacturing machines. Rather than several separate control automation compute platforms operating on a machine, each control compute system can be consolidated into separate virtual machines on a single multi-core compute platform. A typical configuration is shown below:
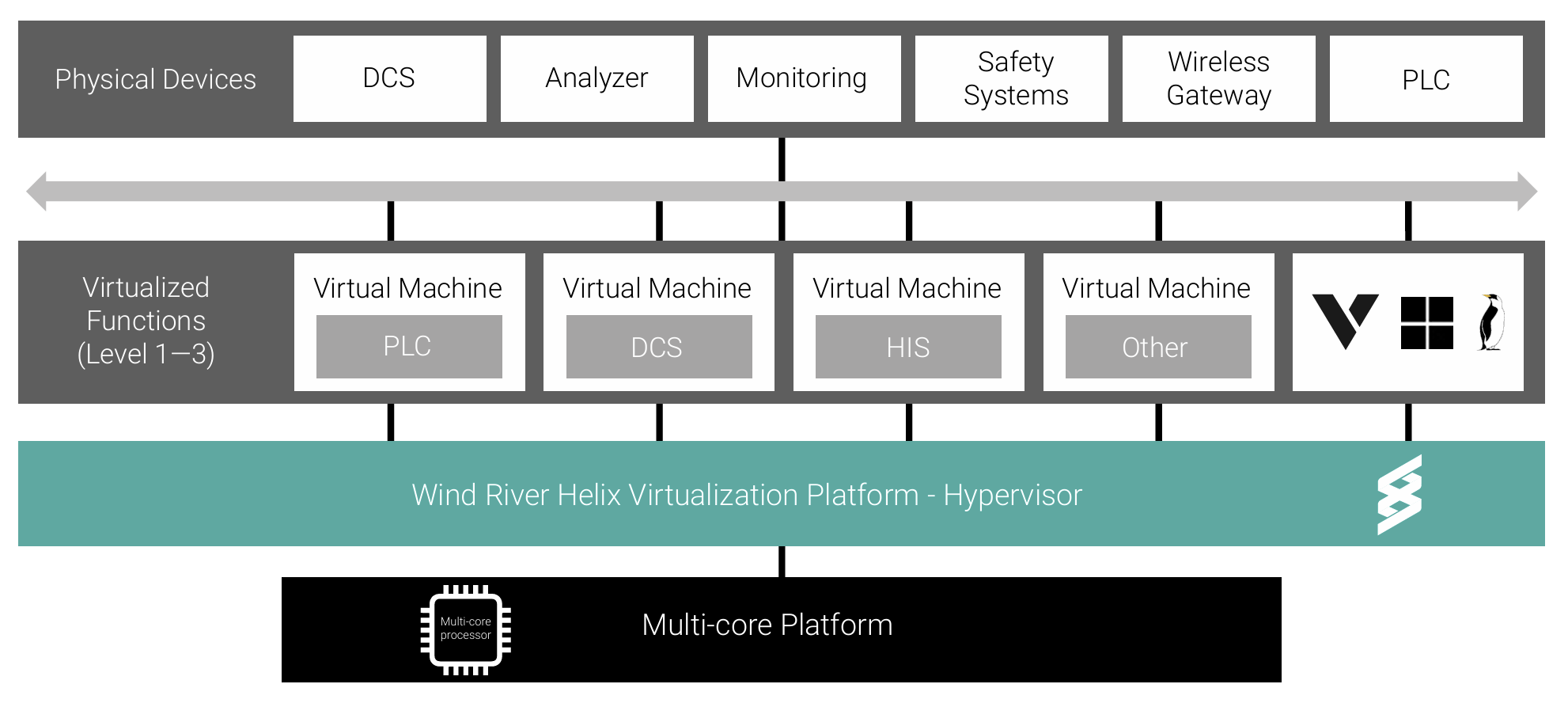
Components of the solution in Figure 1 are:
- Multi-core system (Arm, x86)
- Helix Platform
- VxWorks real-time operating system
- Wind River Linux operating system
- VMs running VxWorks and guest OSes
- Machine 1: PLC control management system
- Machine 2: DCS control management system
- Machine 3: HMI running on guest Windows OS
- Machine 4: Wind River Linux OS running safety, communica tions, analytics, or legacy applications
- Machines 5 and 6: Optional add-ons
To learn more about Helix Platform, VxWorks, or Wind River Linux, visit www.windriver.com, or contact salesinquiry@windriver.com.